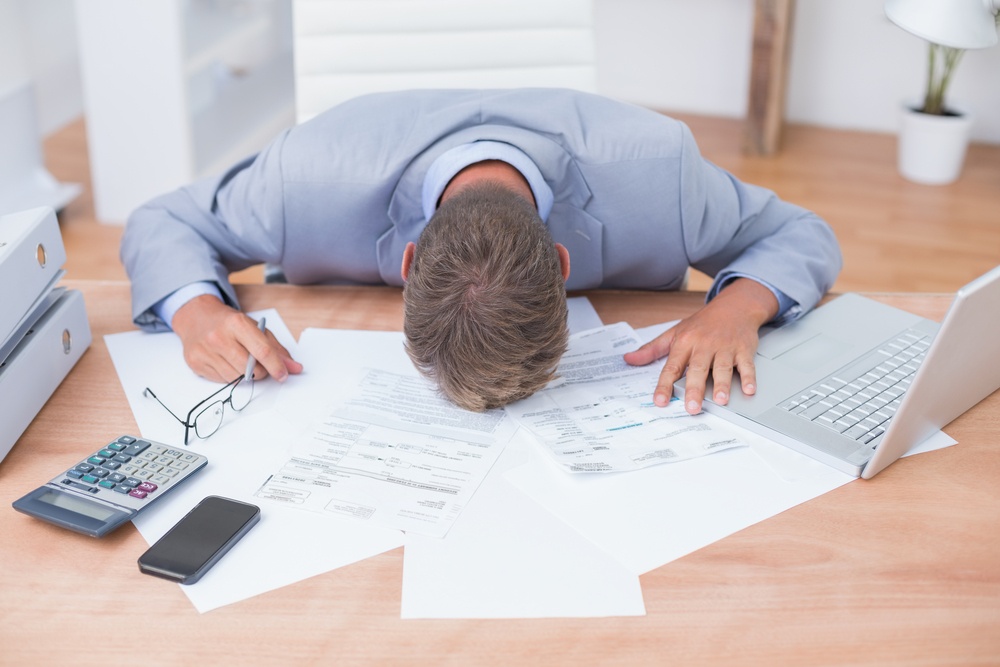
We have analysed on a number of occasions the advantages of making your fleet management automated through specialised technology. If the positive reasons to switch to an electronic system are obvious, it still seems that smaller companies in particular tend to view these systems as only applicable to bigger fleets. But even in smaller fleets, manual fleet management usually has costs that might not be self-evident—this is something that can affect a fleet of any size.
So, what are the costs behind manual fleet management that most companies do not know about?
Here we list the top five hidden costs of manual fleet management:
1. Printing of books and time dedicated to that
Fleet recordkeeping, for example, transport register books or anything related to compliance, such as checklists or logbooks, requires extensive time to be printed and issued which is costly both in terms of work, resources and paper, not to mention being environmentally unfriendly.
2. Administrative work
Validation, collection and recording of paperwork demands substantial administrative resources in order to be carried out accurately—and is still subject to the potential errors that are very unlikely with technological methods of recording .
3. Turning information into data
Following on from the different stages needed to collect information manually, there is still the cost of all the work involved collating the information and compiling it into data that can be of practical use later. With the added disadvantage that the information recorded manually can still be subject to human error or remain obscure, so that the end results are unreliable and of little benefit.
4. Storage cost
If everything is logged on paper, imagine the volume of documents your company has to deal with and how time consuming it is to file and also to access quickly when needed—a world away from the peace of mind that comes with knowing that all you’ll ever likely to need is available in just a few clicks of a button.
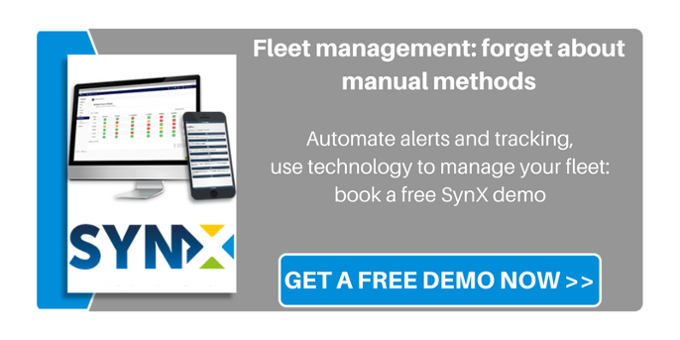