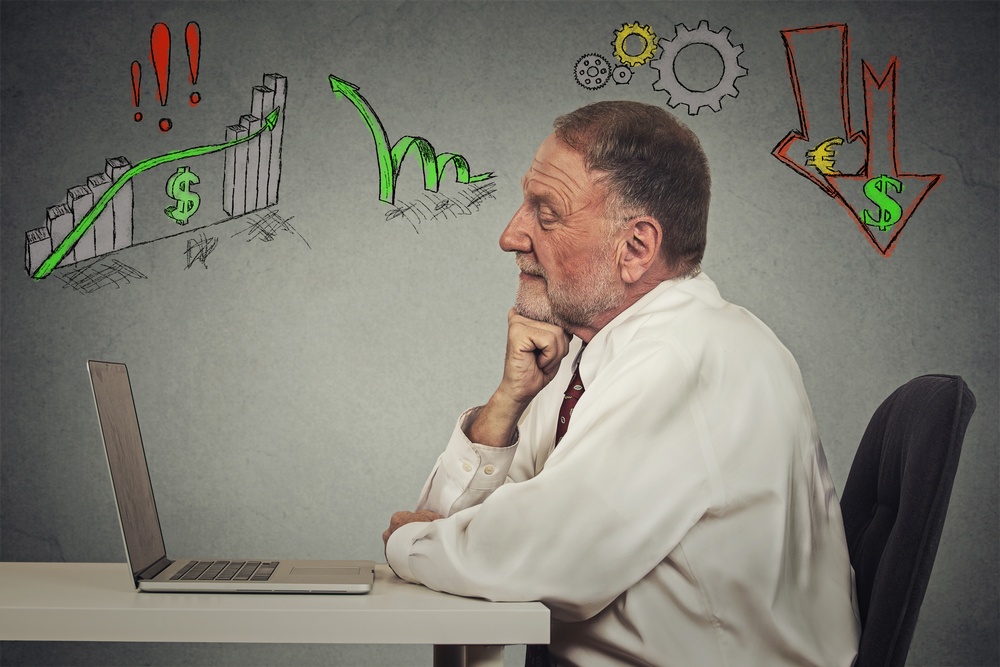
In order to get a positive global company performance, teamwork and cooperation are essential in every sector or activity. Fleets and businesses that depend on driving follow the same rule; and if on one hand the budget and the physical resources are important, on the other hand you cannot rely on those alone to achieve fleet success as the contribution of the whole team and all of its individuals in their roles is equally as important.
Getting the buy-in of your employees and team and making them your best allies is not easy; but if you follow some basics, you can make this happen, and this would be the first step towards ensuring your company complies with the budget and creates savings. Here are 4 actions you can take to that effect:
#1 - Use a reliable system to record the global performance of your team. There are a wide number of applications such as fleet management software that are able to help in evaluating the performance of your team thanks to the increased visibility and the metrics tracking that they offer. Your employees might be mostly perfectionist or mostly safe in temperament, but if you are able to detect more deeply the way they perform, you can make good on past errors, help them improve and achieve good progress; something they themselves would definitely appreciate.
#2 - Propose to set up targets for performance improvement. If you have access to the performance of your team, you can focus on strengths and weaknesses and encourage employees to mutually collaborate: to initially complement one another, to learn from the good attitudes of their workmates or even from mistakes that they may commit but might be unaware of. The key is grasping what the real situation is, analysing it and setting objectives to improve as a whole, which in the end might lead to savings or global improvements.
#3 - Make sure everything is communicated and knowledge is shared. When some internal processes change or anything new comes up, it is necessary that everyone is informed. But this becomes even more important when some things happen, such as an accident, a maintenance problem that is not detected on time, or a fleet issue. The idea is not to point out who’s responsible but actually to learn from the mistake or from a process that might not have been dealt with correctly or should be partly changed—the purpose is to detect the causes of the error in order to avoid more in the future.
#4 - Write rules down in black and white. Putting everything on paper does not necessarily only refer to compliance lists or fleet policies, though both are extremely useful tools to define rules for employees, they refer to maintenance and much more. If you are following points 2 and 3, it might be extremely useful to recap everything and put it in a written format, with communications addressed to the group as a whole so that everyone understands potential issues or errors and is then able to prevent them.
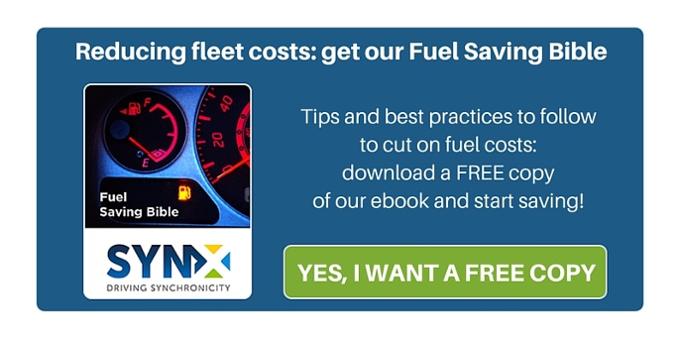