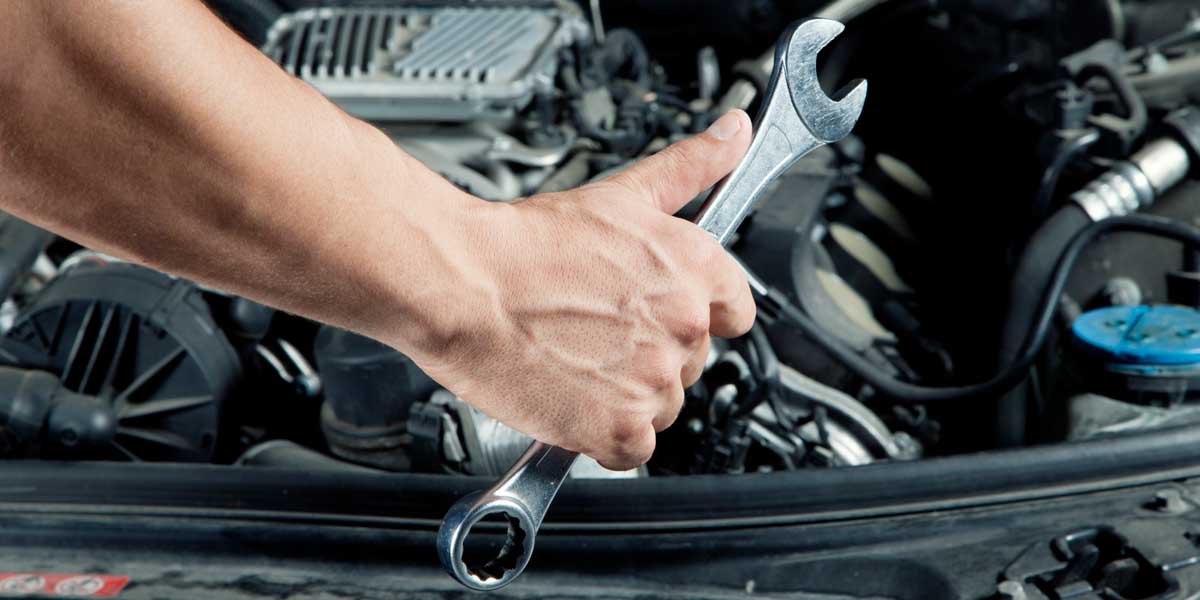
You have surely heard or read the old adage “An ounce of prevention is worth a pound of cure”. This, now common, expression originated from Benjamin Franklin, who coined the phrase when he wrote a short essay about how to prevent house fires. As he noted, it was much less expensive to practice fire safety than it was to rebuild a house that had burnt to the ground.
If we look at the saying and its meaning, we notice some of the obvious advantages of prevention over cure, as
• it is better to try to keep a bad thing from happening than it is to fix it once it has happened;
• it literally prevents the discomfort and costs of experiencing a preventable, negative event.
• it's easier to stop something happening in the first place than to repair the damage after it has happened.
Now let’s consider how Benjamin Franklin’s words of wisdom from the eighteenth century could apply to something as modern as fleet maintenance… particularly the eternal debate on whether to opt for preventative maintenance (prevention) or reactive maintenance (cure):
Some might argue that reactive maintenance allows fleet managers or anyone in charge of controlling a fleet to address an issue once it happens, thus optimising time and focusing on problems only when required. But the truth is that an event such as a breakdown always causes unanticipated costs (try to think not only about the cost of repairs or vehicle replacement, but also the delays it can cause and the workforce downtime to mention just a few) and disadvantages for a company.
A preventive approach seems in the first analysis as more time consuming, since preventative maintenance is based on a series of regular checks and servicing, scheduled according to a combination of factors: type, make and model of vehicle and manufacturer’s recommendations, scope of the vehicle and company’s activity, the weather in operational areas and so on. But in actual fact, a preventative maintenance philosophy offers advantages in a breakdown, such as a faster and more active response with a deeper knowledge of each vehicle and of the likely reasons which might have caused the breakdown itself. And it eventually results in lower costs as well…
In terms of fleet maintenance best practices, what do you think, which attitude would you recommend? Preventive maintenance really seems to be the best option. But how would you organise a preventive maintenance system? What would you use in order to decide how to plan servicing for your vehicles? If you need help with that query, have a look at our software page and see what SynX Perform can do for you!
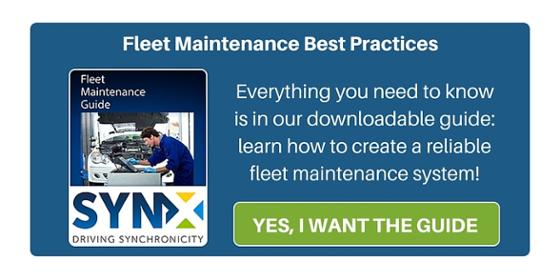