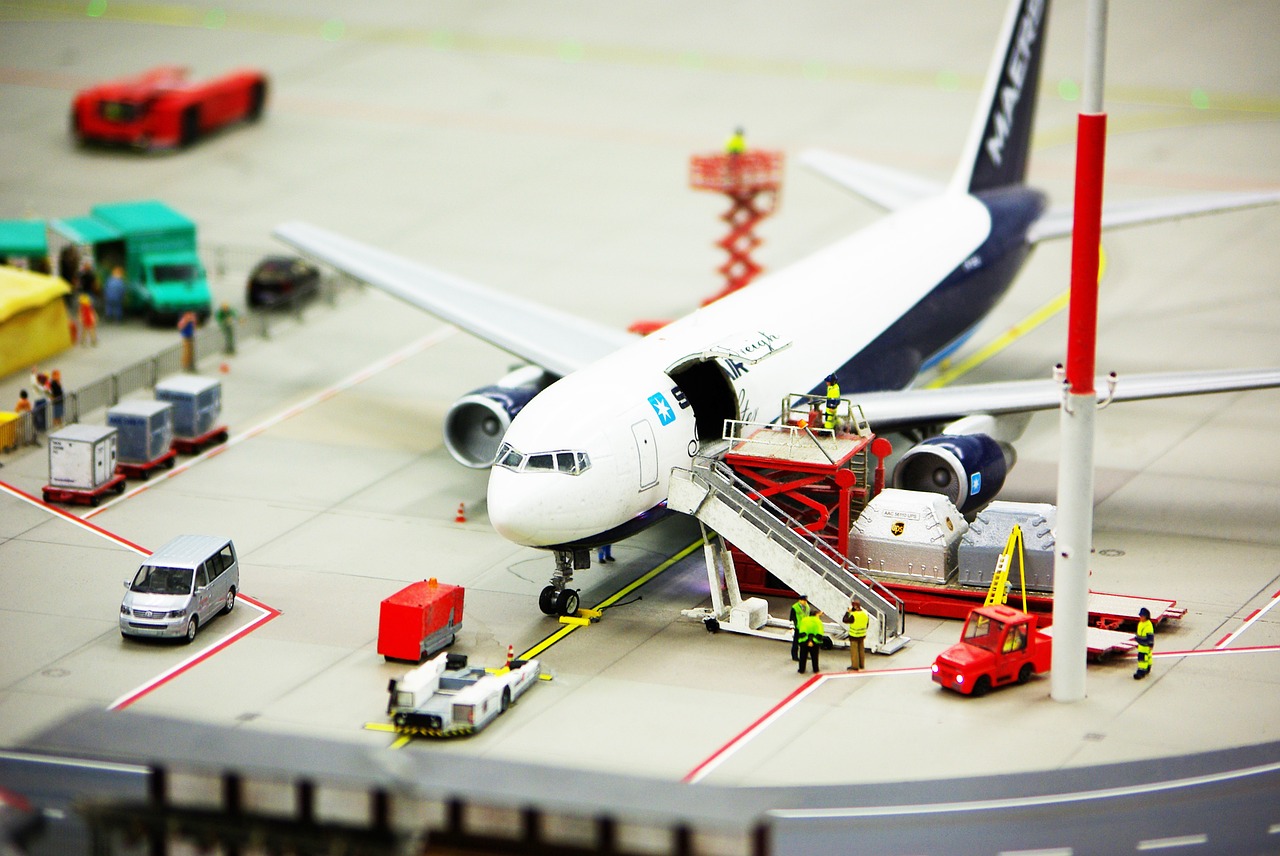
Operating Ground Support Equipment Fleets is anything but easy. Daily ground support operations are carried out in fast sequences with very low room for mistakes, as these can lead to costly delays. The most diverse activities are carried out on the ramp, from vehicle maintenance to aircraft refueling, from de-icing (when necessary) to baggage management.
In such a demanding and fast-moving environment, ground handlers have to consider cost savings as one of their top priorities without endangering compliance and safety of passengers and workers. But there are some sound principles that, if followed, can still allow ground handlers to spare money. Let's have a look at them.
#1 Choosing the right vehicles. Vehicle choice is something that should happen after thorough consideration. In some environments, electric GSE can prove to be more efficient than diesel-powered equipment, and viceversa. The adoption of a vehicle can be justified despite high acquisition costs if proving to be more suitable for your type of procedures compared to another. A specific vehicle might not be perfect for anyone, but there is a great deal of data you can obtain from your assets that can help you make the appropriate decision in terms of savings and efficiency.
#2 Keeping vehicles in working order. Scheduled maintenance as well as daily vehicle checks are always the best way to save money down the road by avoiding last-minute servicing or costly rushed parts shipping. Unexpected repairs can be avoided by building a personalised maintenance calendar based on the actual needs of your GSE fleet, its actual working hours and performance.
#3 Getting the entire perspective. Before making important decision it is necessary to consider the overarching story of your fleet. If you can count on an accurate big picture view of your operations, identifying unnecessary costs (as well as unrevealed saving strategies) will be much easier.
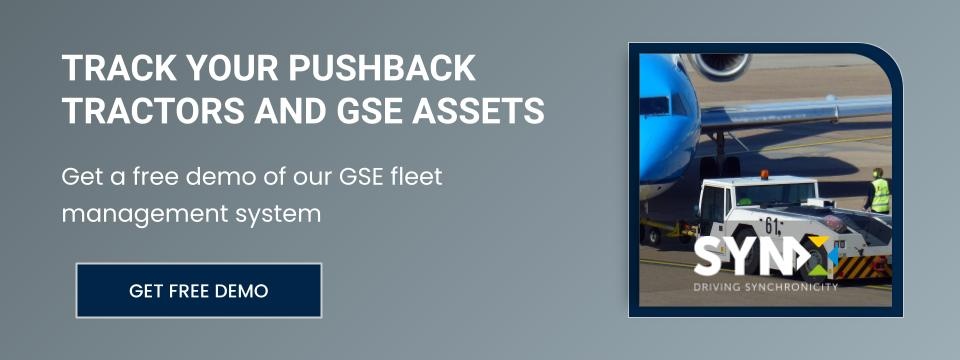